Design and Engineering
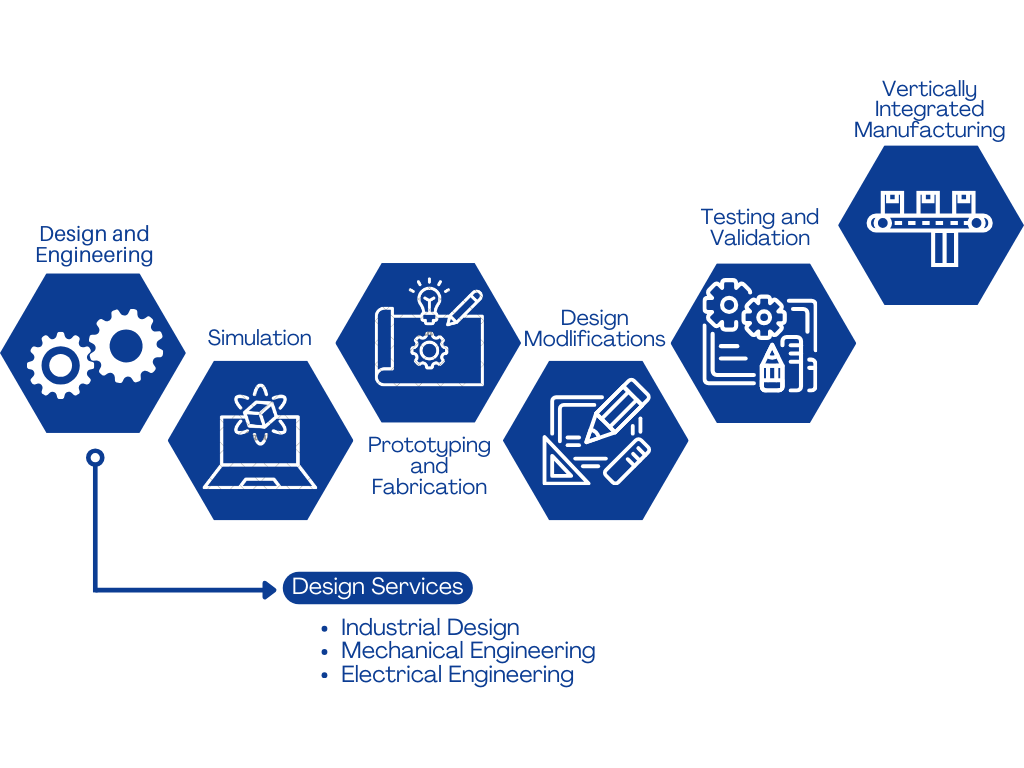
Design and Engineering
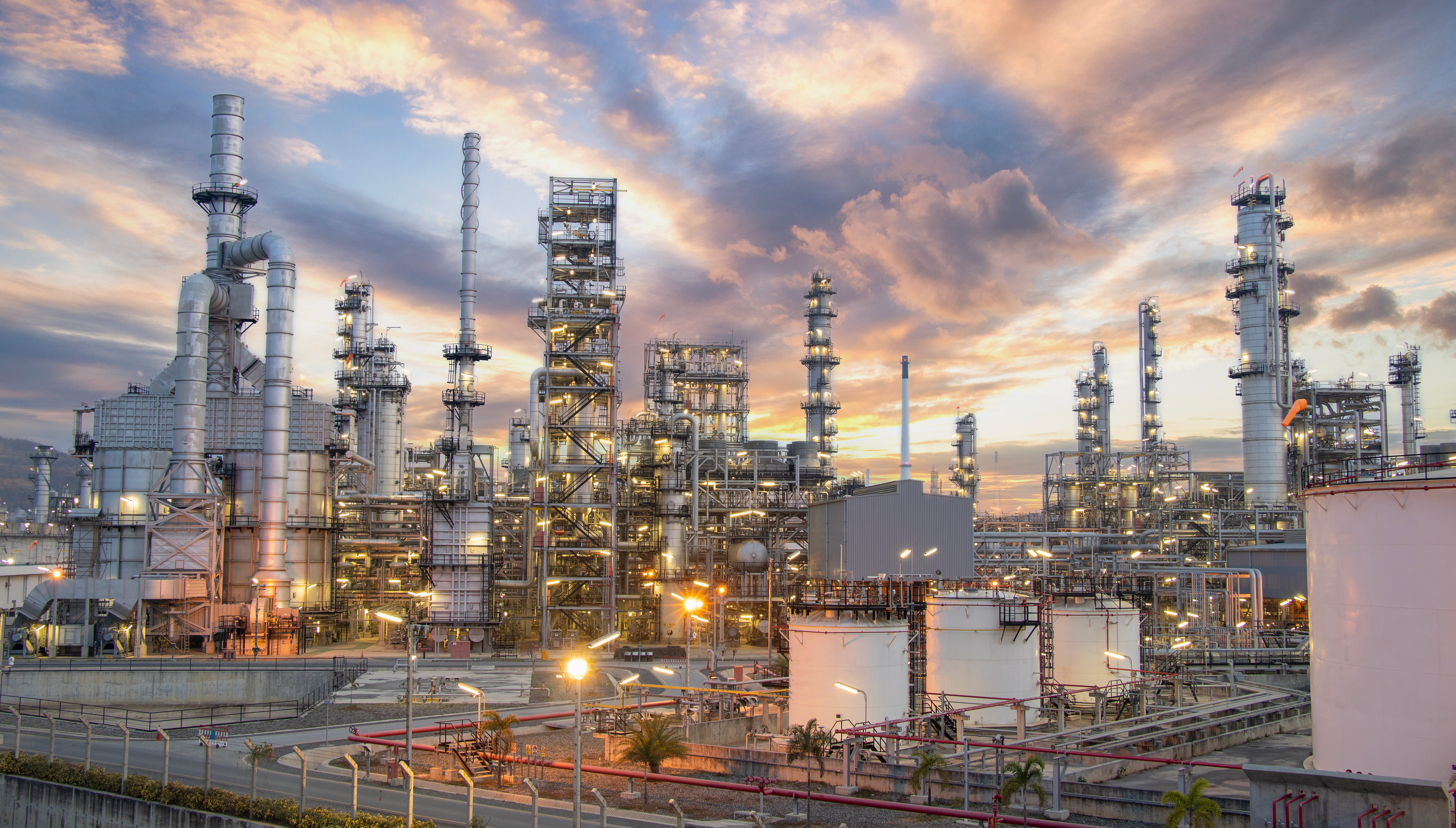
Industrial Design
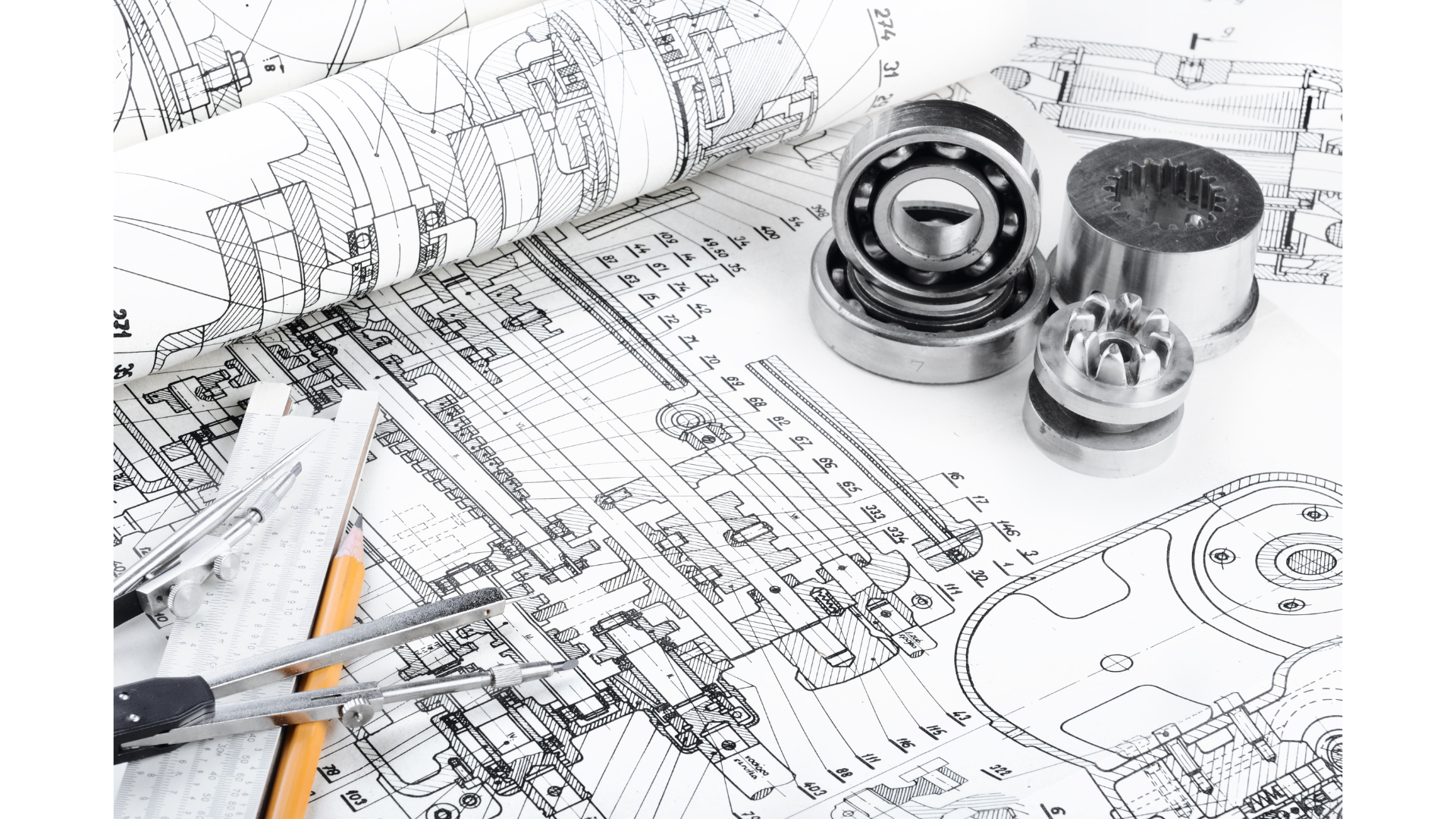
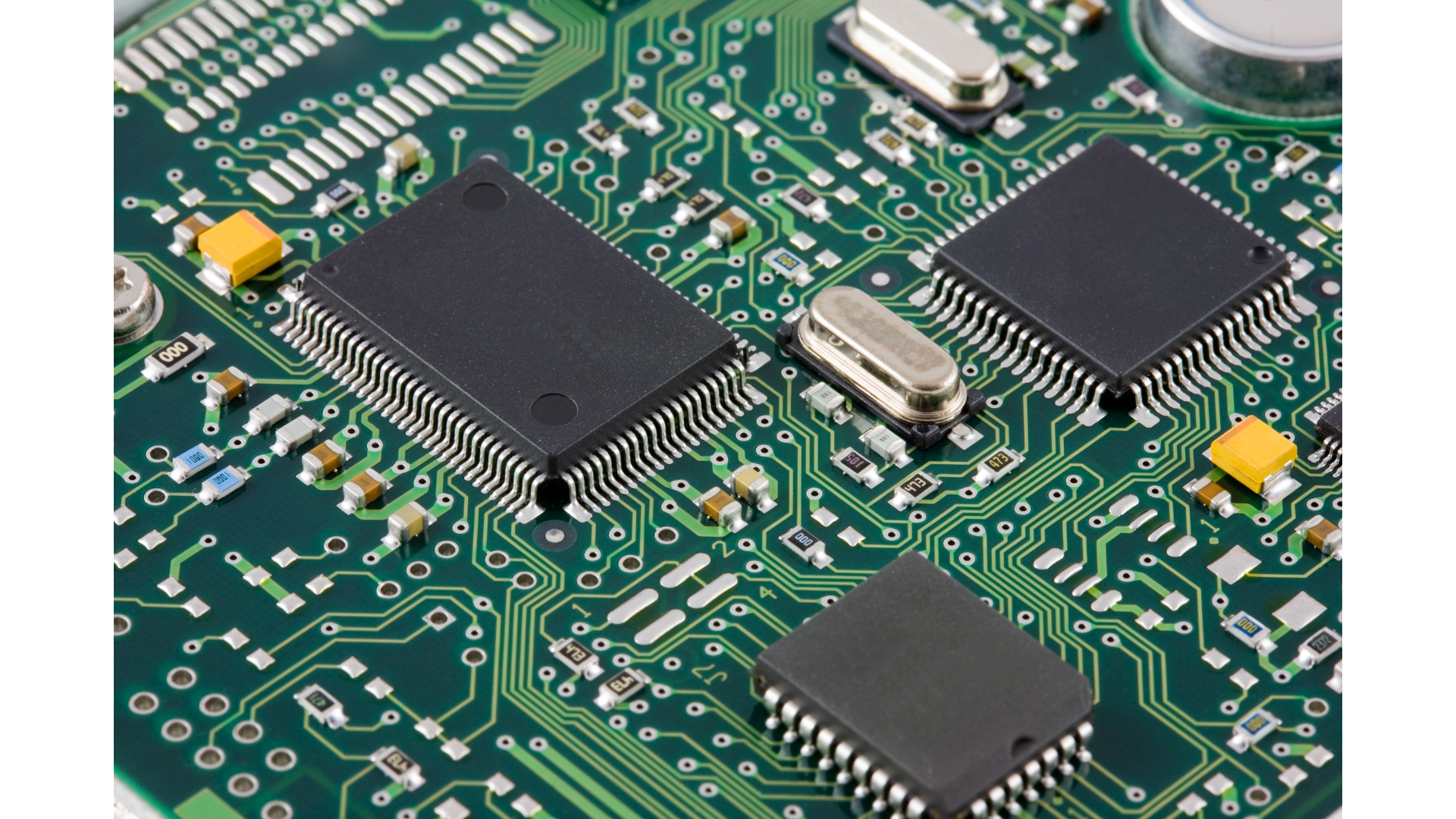
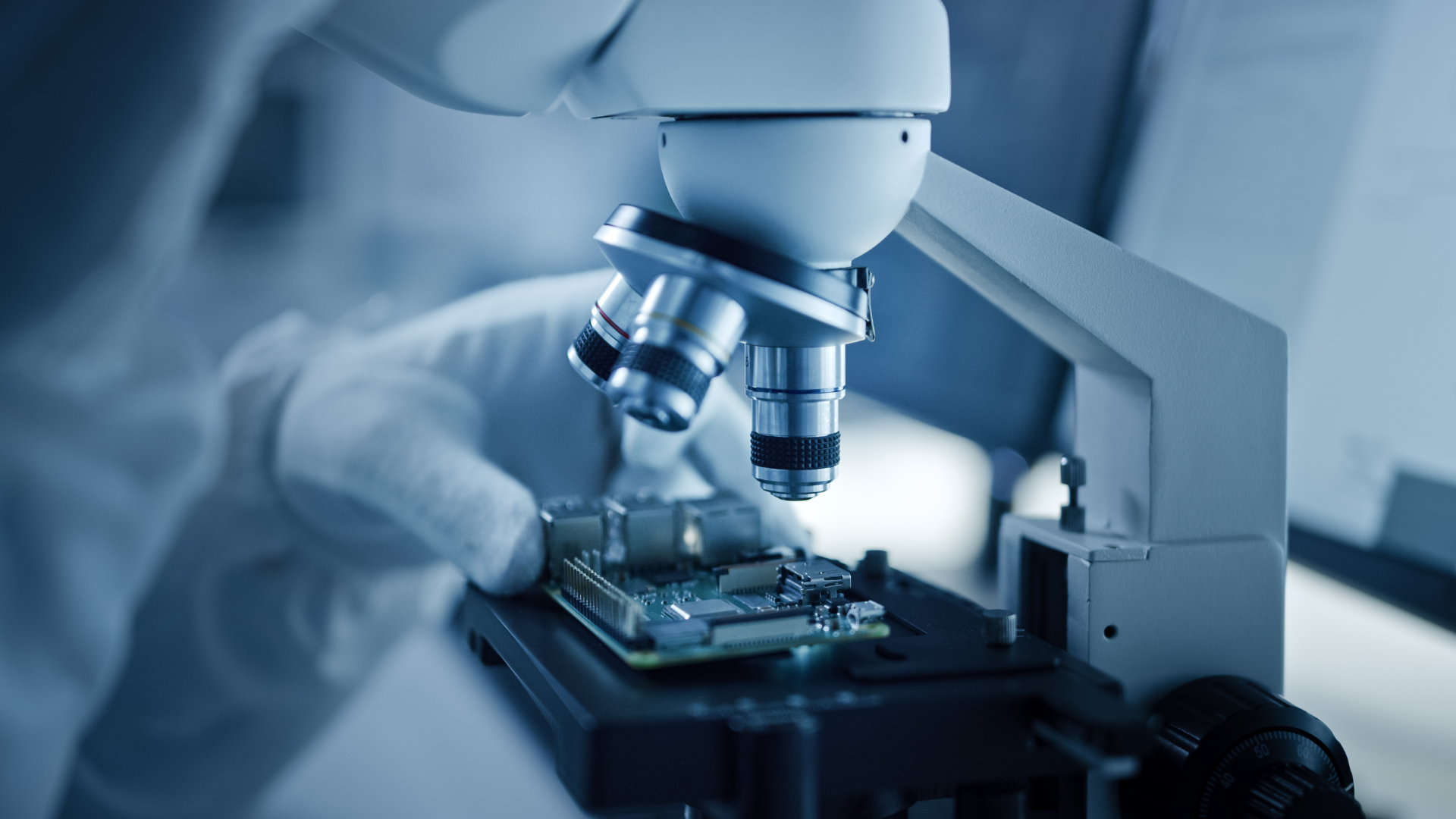
Industrial Design
As a vertically integrated manufacturer, beginning from the initial concept development phase, our experienced ID designer communicates across different engineering specialist teams, especially with our manufacturing unit to ensure the defined form factor can be well-executed in the following manufacturing processes.
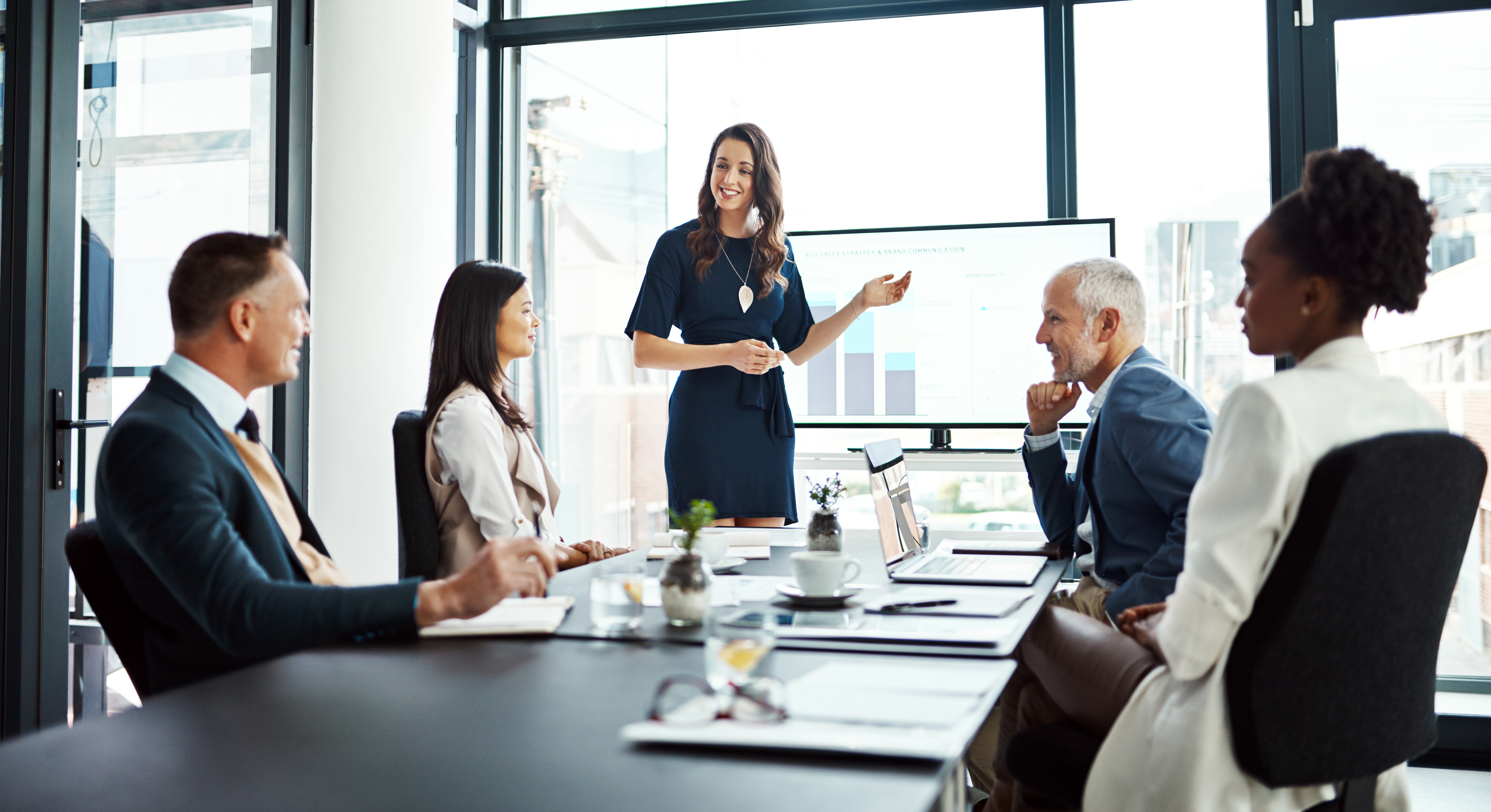
Concept Development & Proposal
(Form & Function)
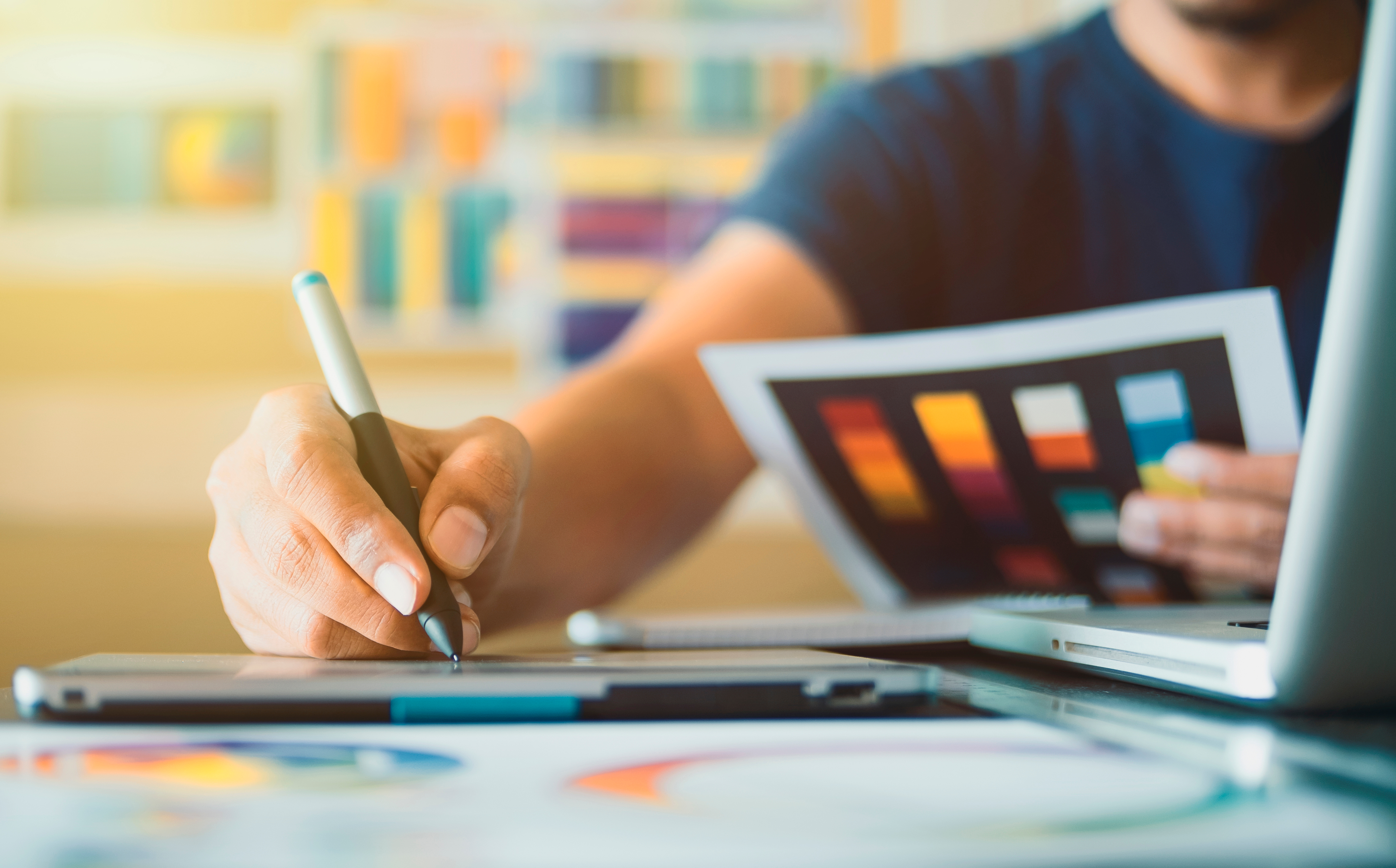
Visual Design
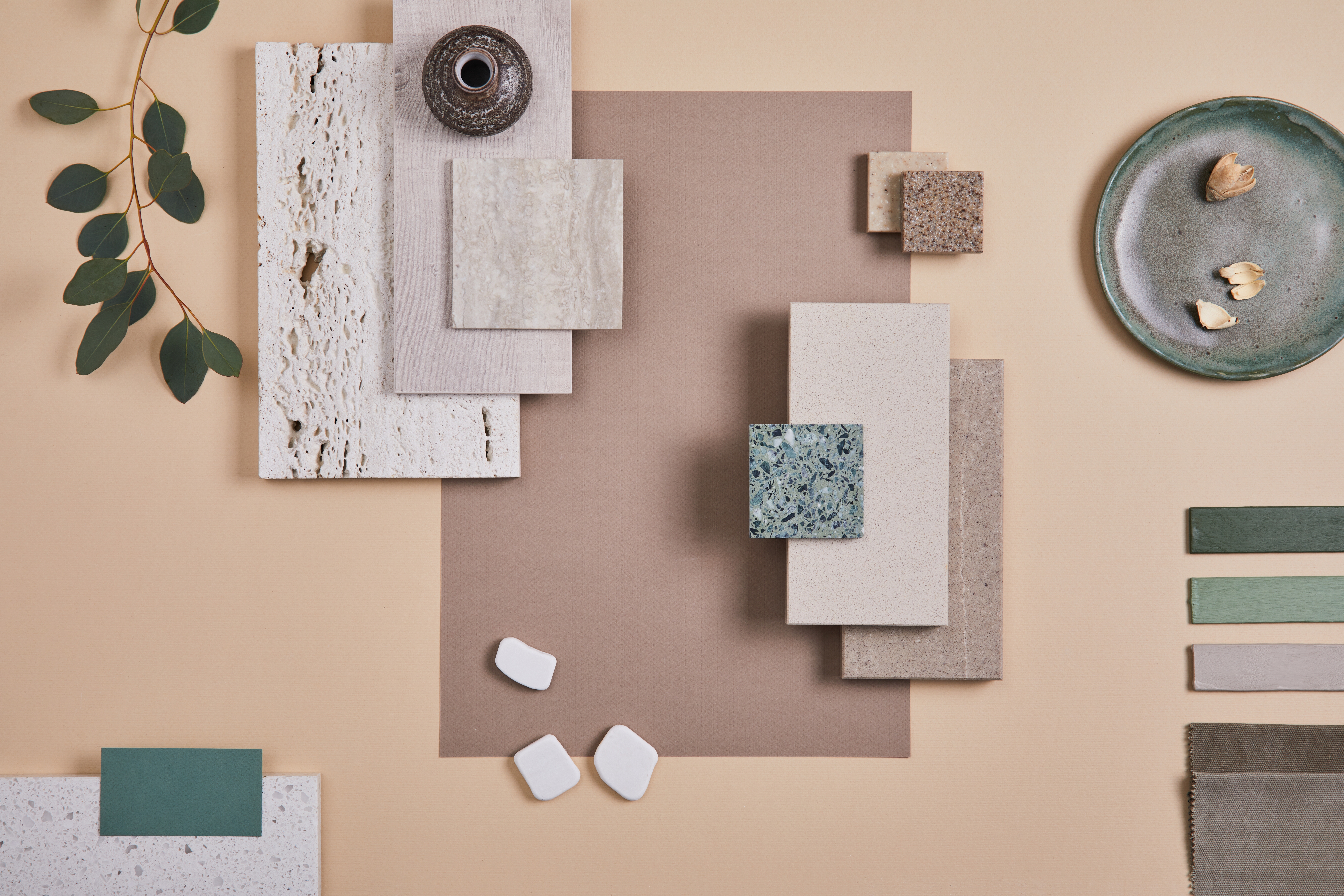
Surface Details
(Colour, Material & Finish)
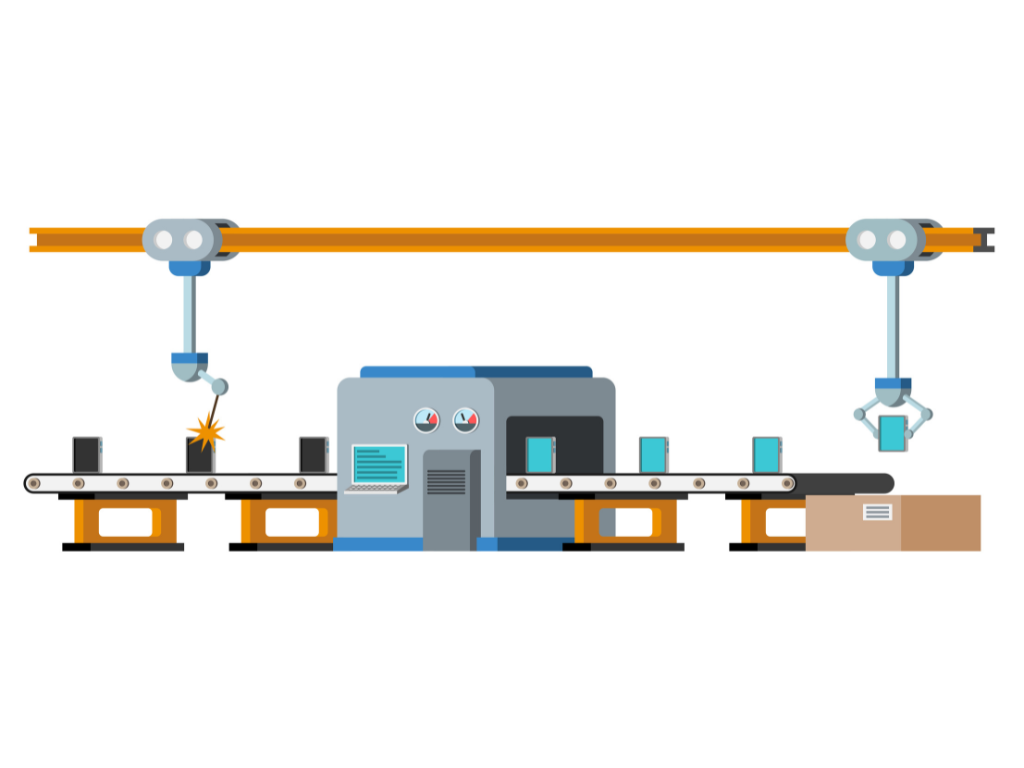
Packaging Design
Mechanical Engineering
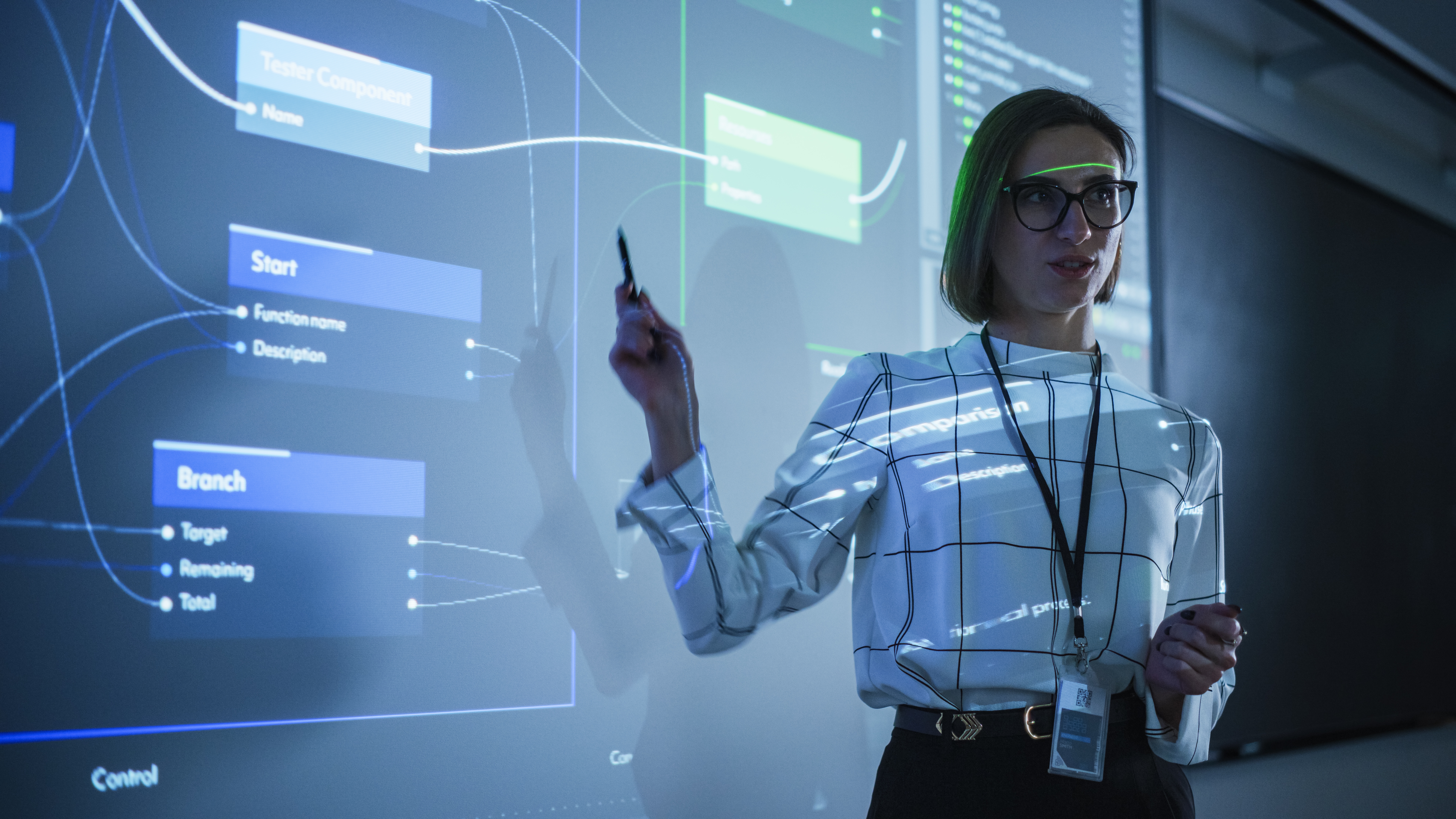
Product Architecture & Function
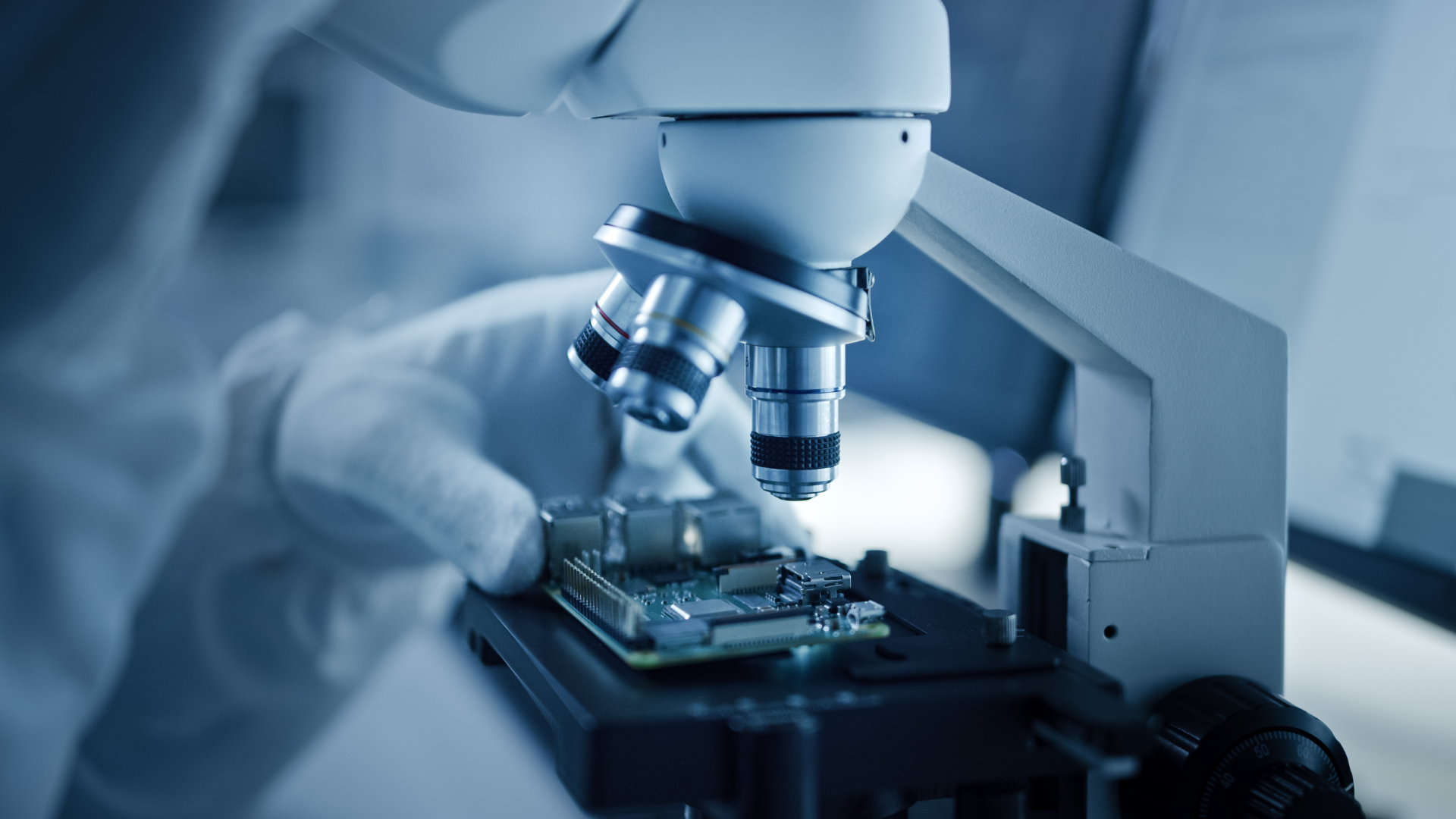
Reliability Test Requirement
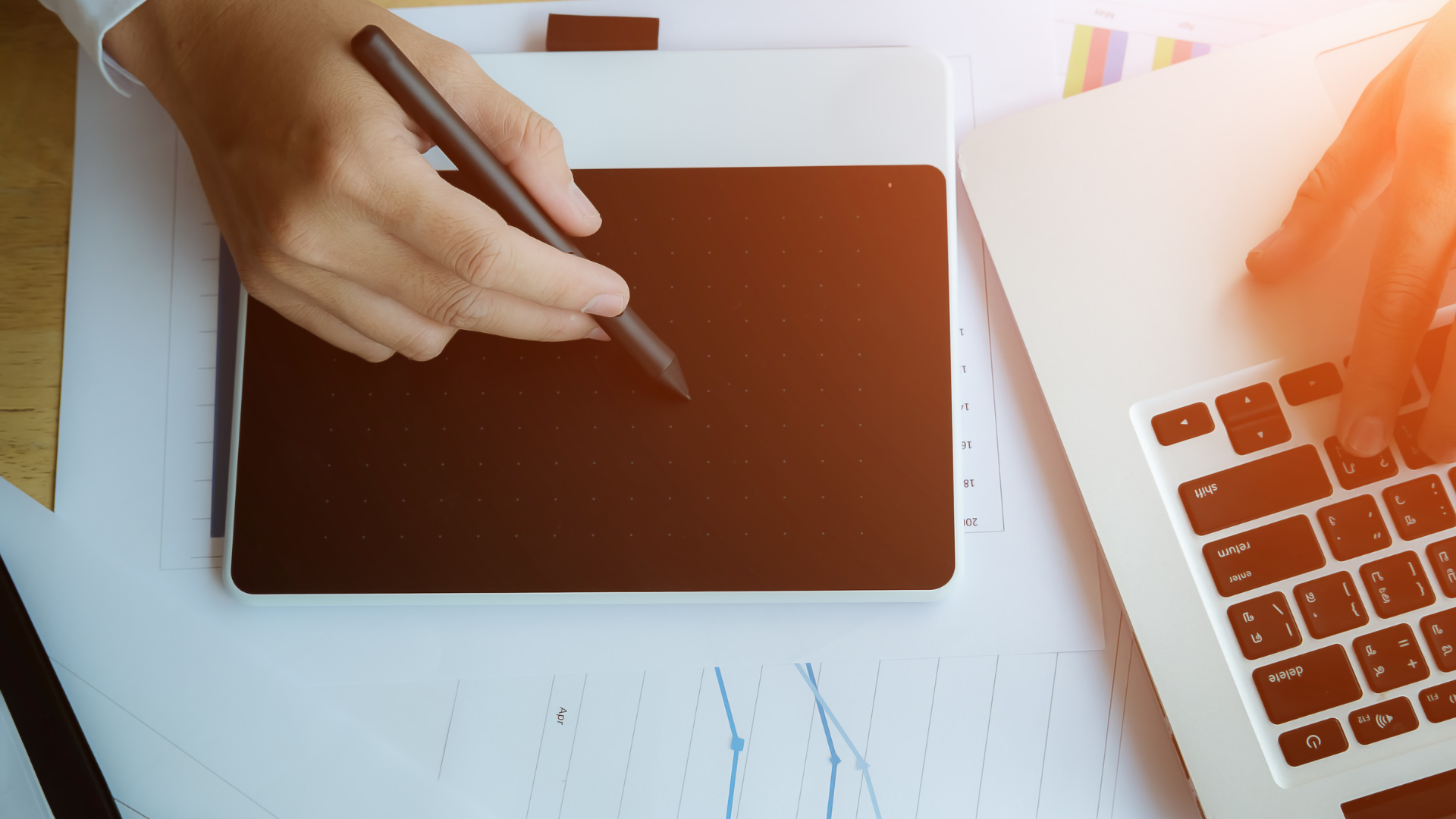
Tooling Design & Development
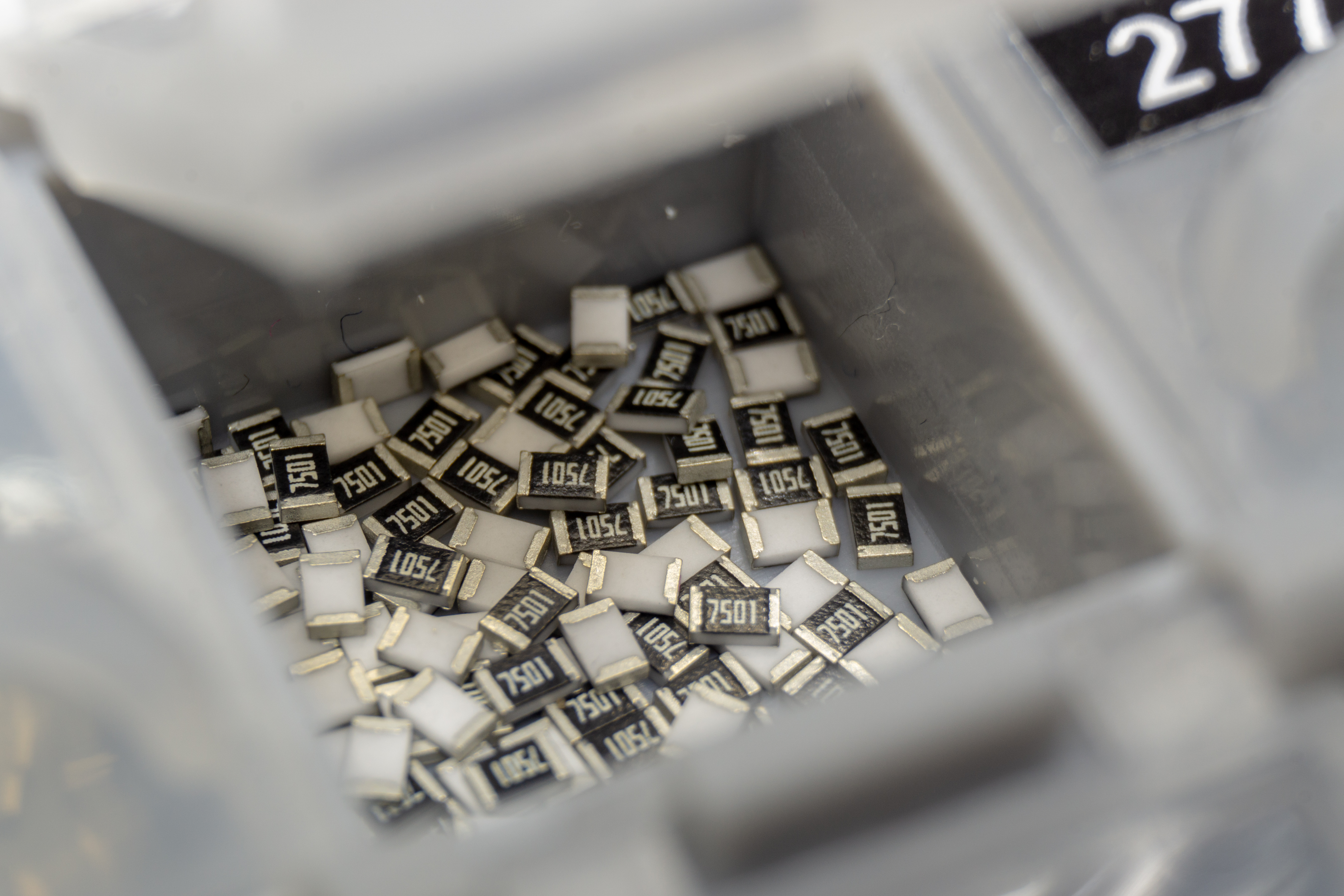
Material Analysis & Selection
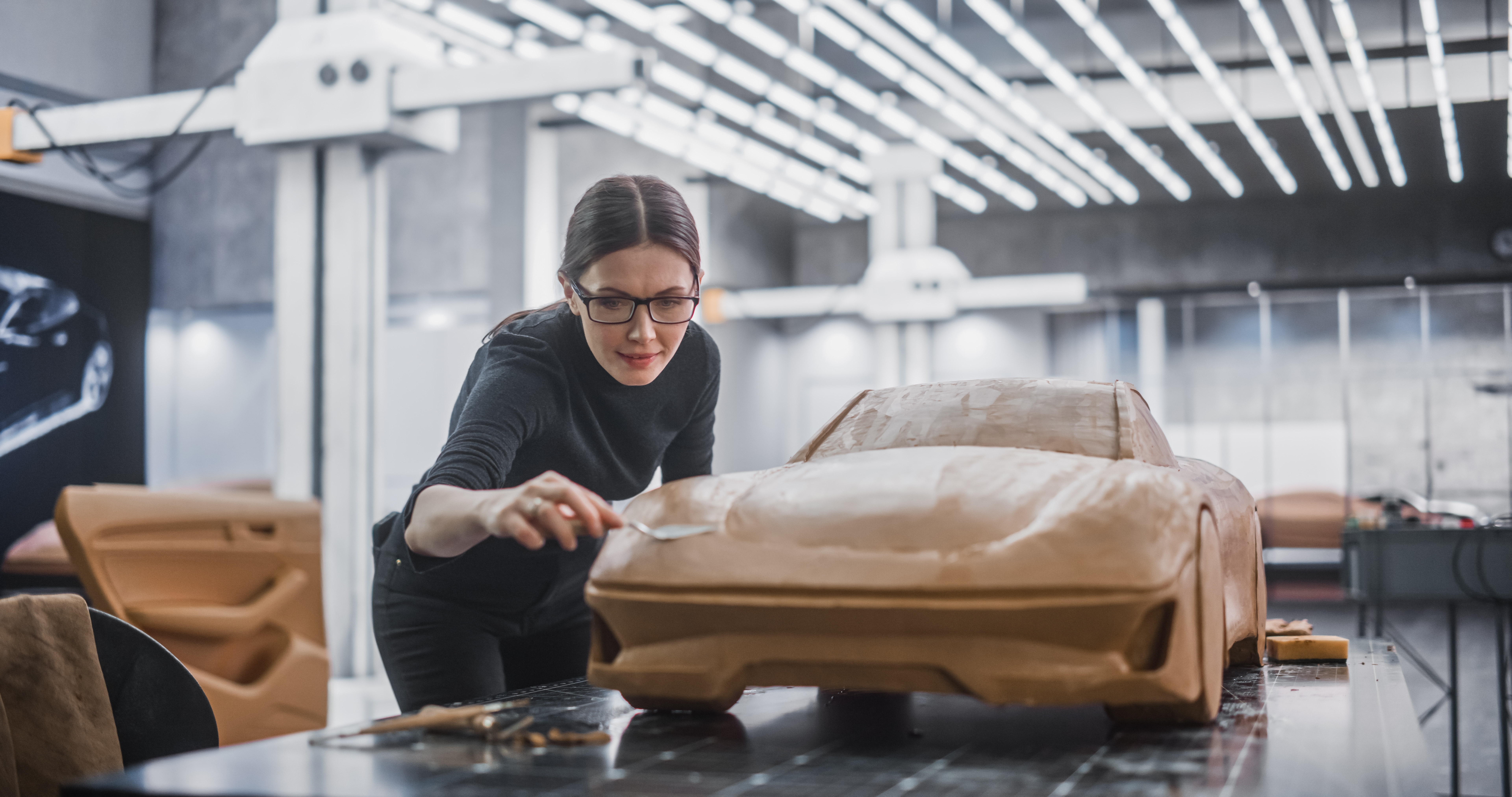
Prototyping & Concept Validation
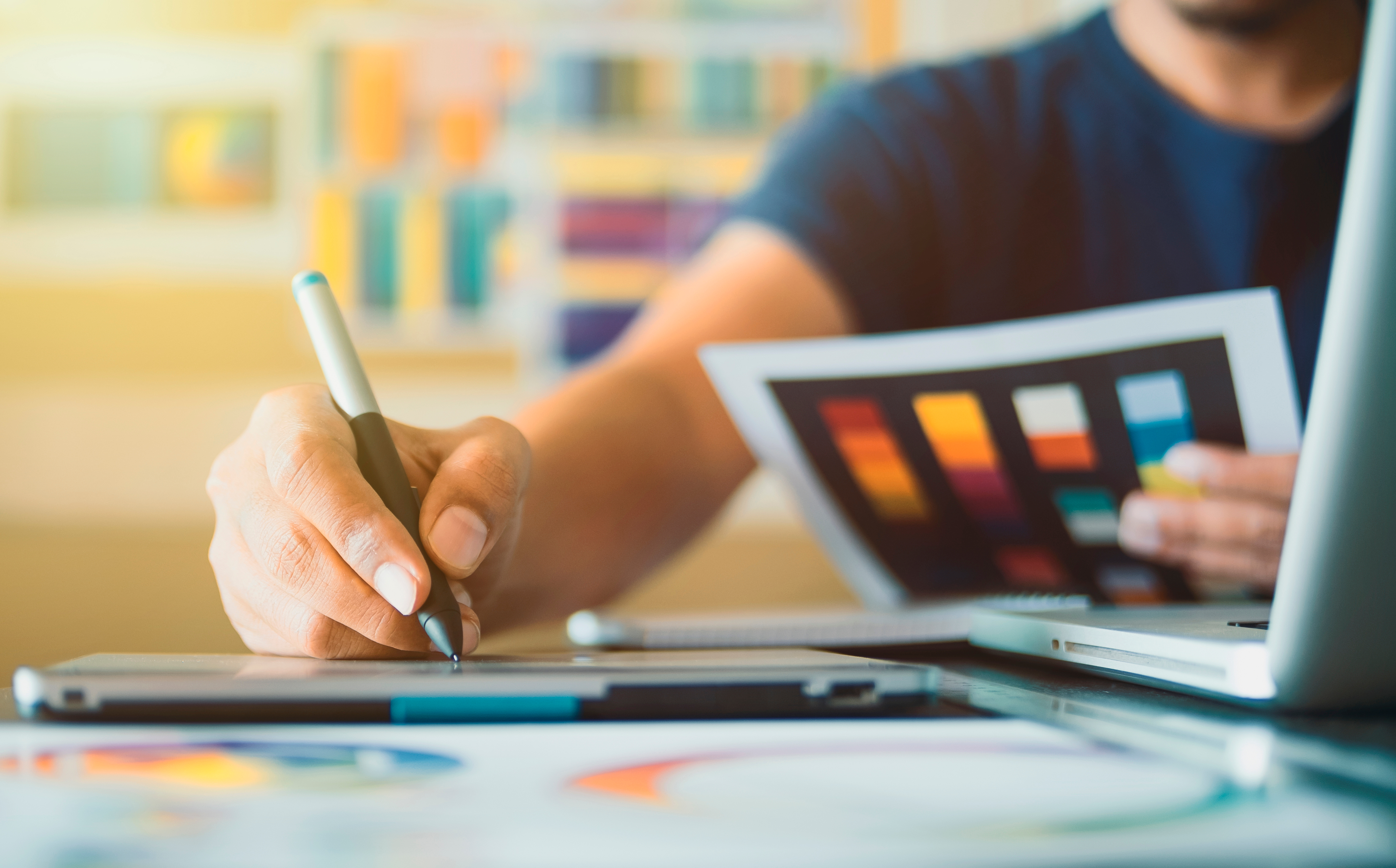
Design For
Manufacturing
The overall mechanical architecture and detailed design of product requirements are created after thorough discussions between our customers and related cross-functional teams.
From meeting defined functionality and thermal ventilation to testing specifications and mass production feasibility, our mechanical engineers achieve these through following core design principles and incorporating extensive manufacturing experience. Further supported by comprehensive technical analysis using advanced assisting tools such as Computer-Aided Design (CAD) and Computer-Aided Manufacturing (CAM) to facilitate early development processes and DFM before official tooling development.
Electrical Engineering
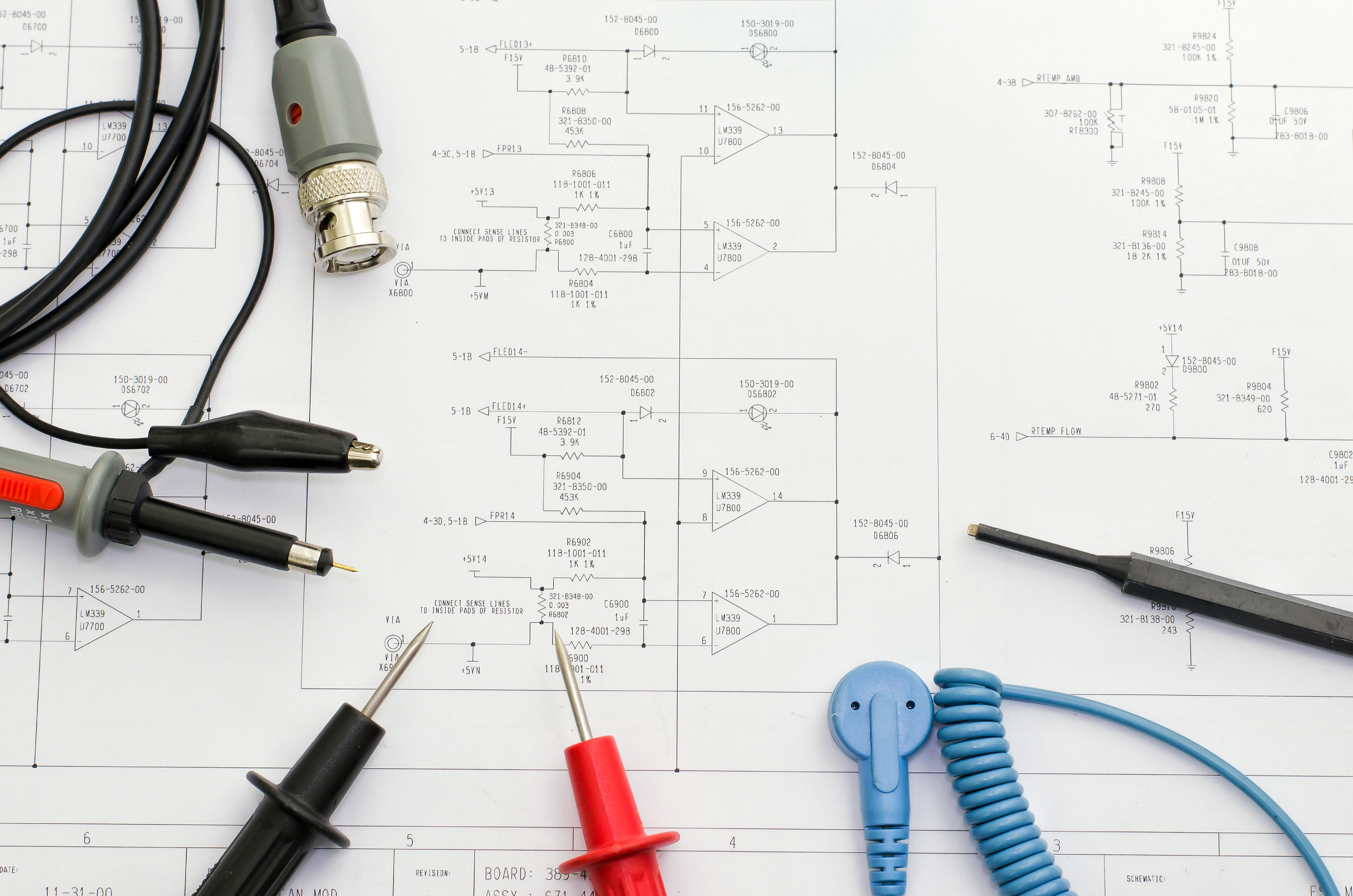
Schematic
Design & PCB Layout
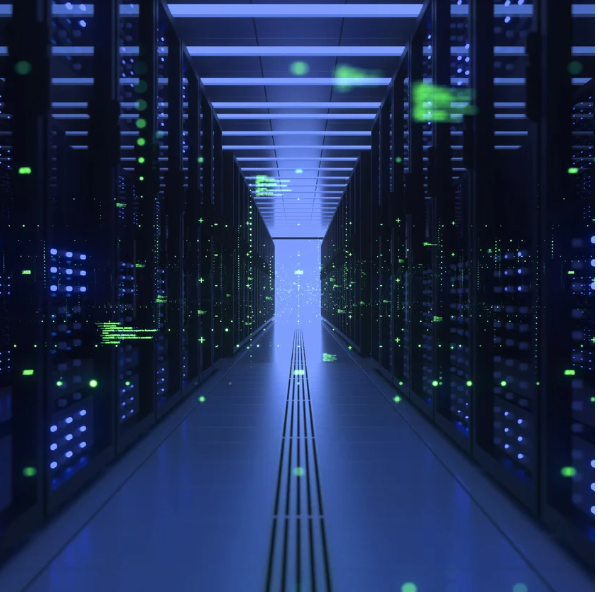
High Speed Routing
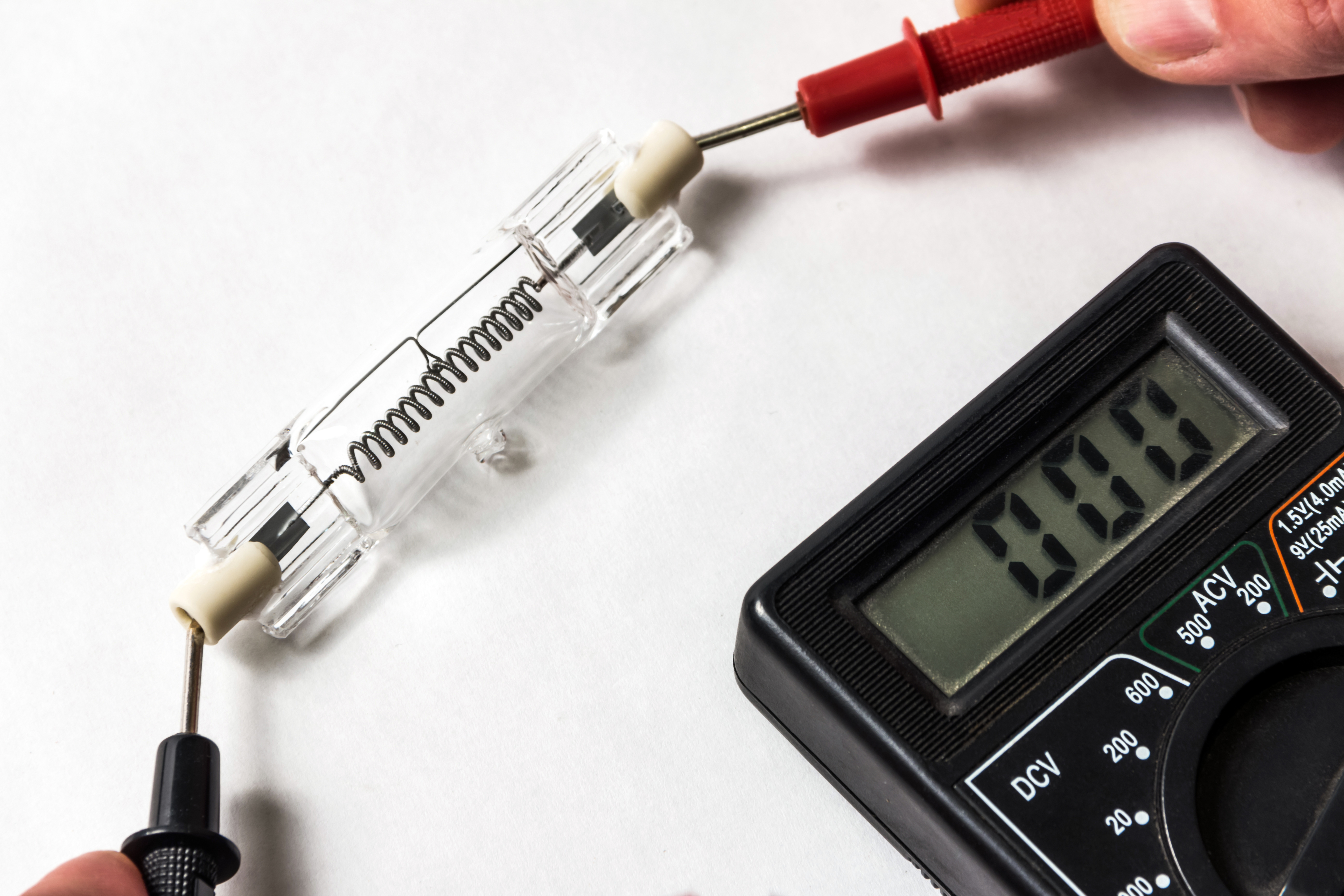
Testing Fixture Design
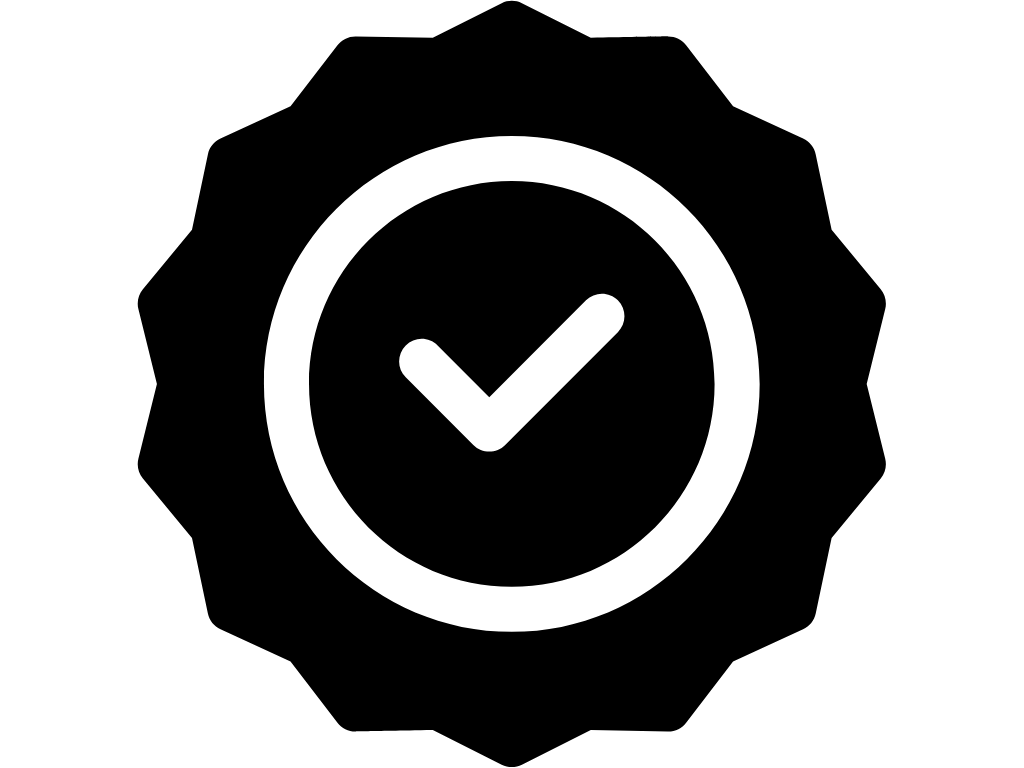
SI Verification
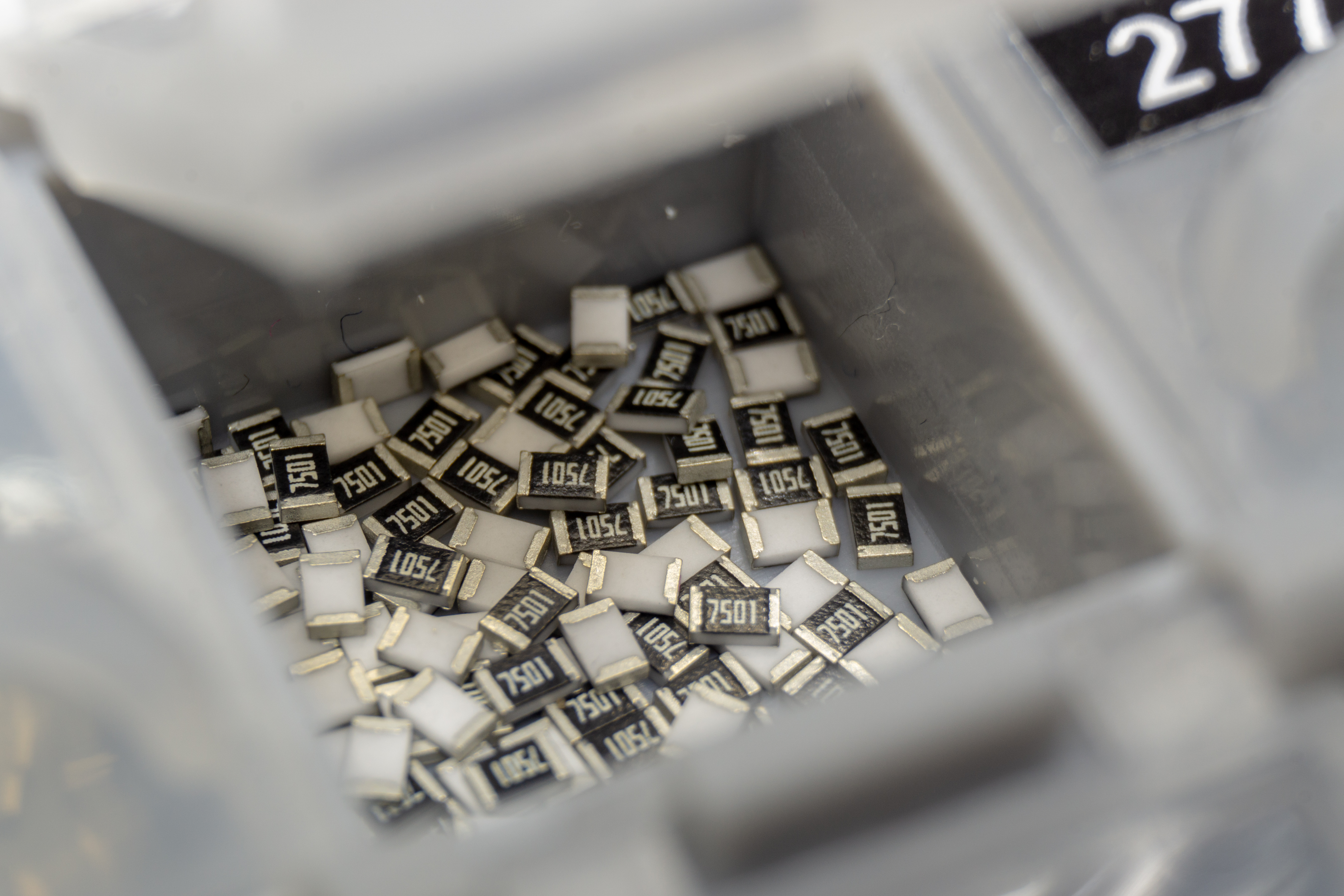
Component Selection Recommendation
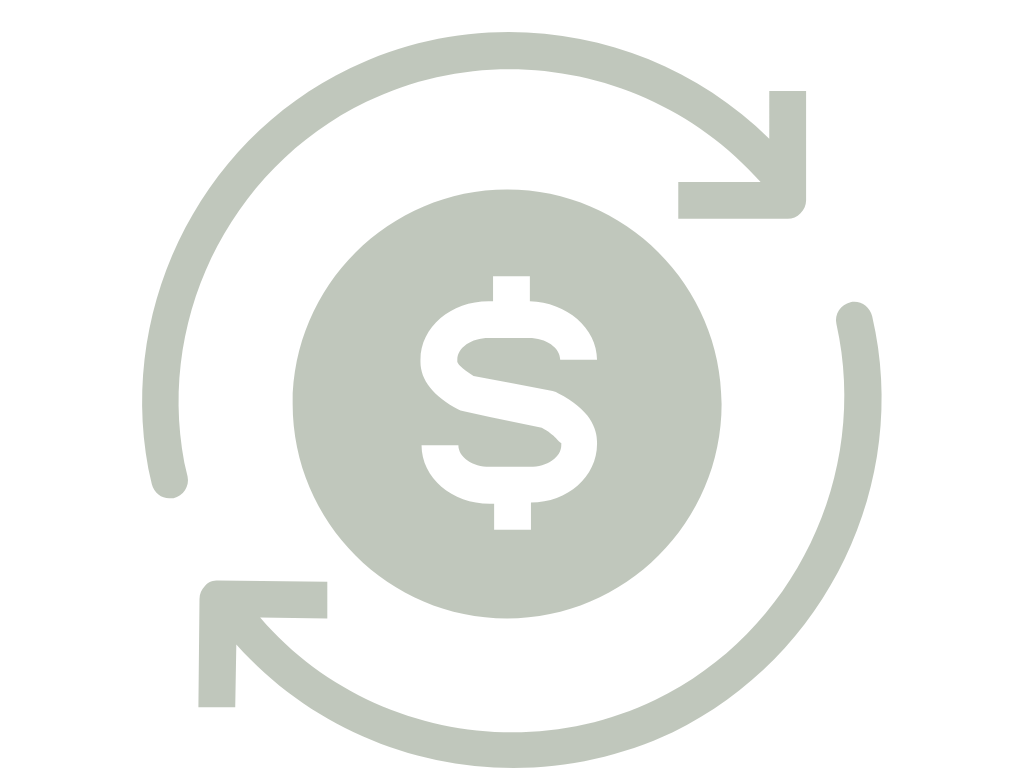
Cost Optimization
Given the technological advancement and ever-increasing demand for bandwidth with minimal signal interference, our engineers are experienced in working with products from a range of applications but not limited to Consumer Electronics, Automotive, Industrial, Medical, and Aerospace.
At Rayo, our electrical engineers are highly experienced in providing high-speed and high-frequency designs. From the initial block diagram, PCB circuit design and layout, to overall system architecture definition, we will work closely with our client to ensure the design reflects requirements at each key milestone.
Fabrication and Assembly
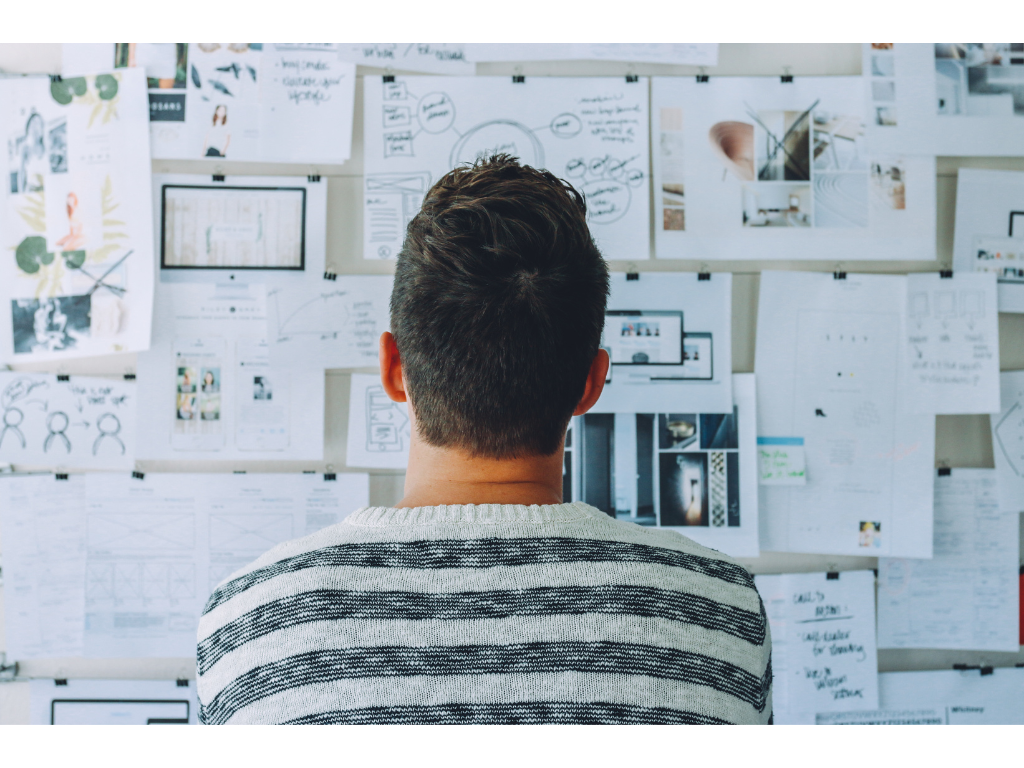
Concept and Product Validation
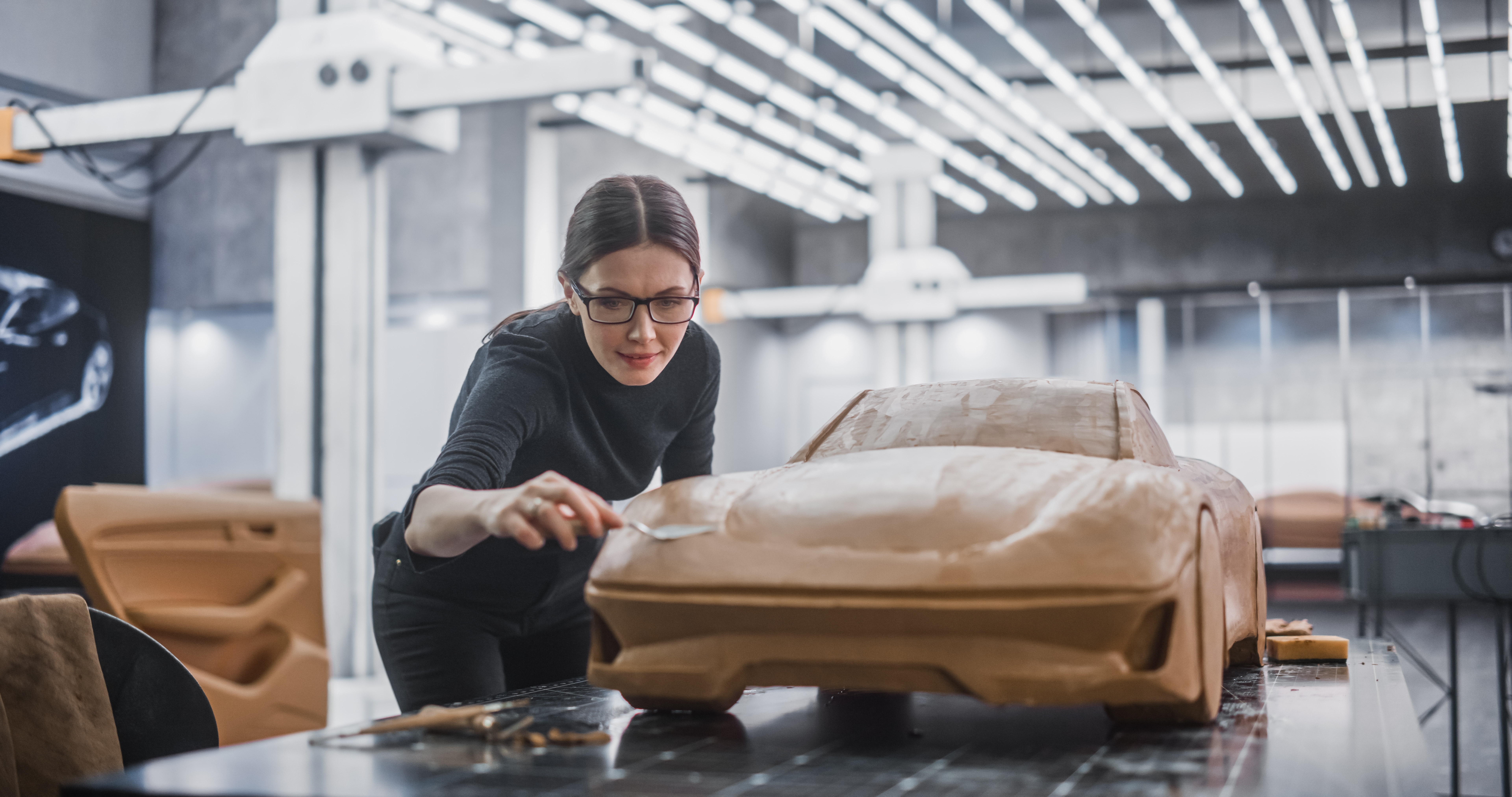
Prototype Creation
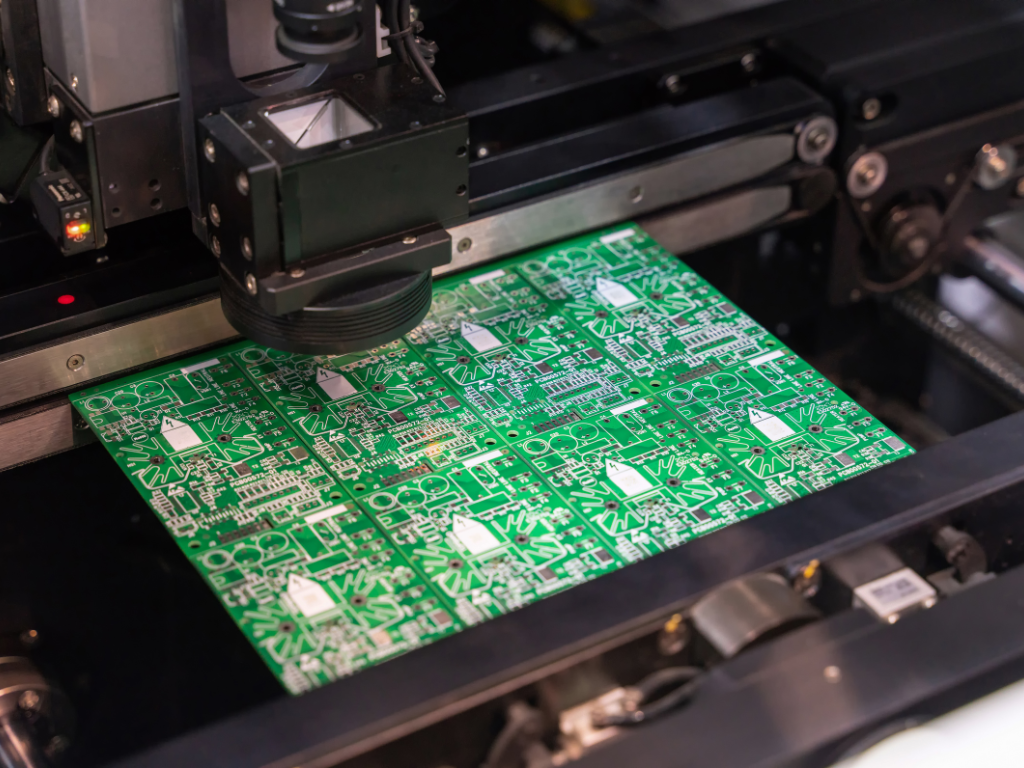
PCB Fabrication and Assembly
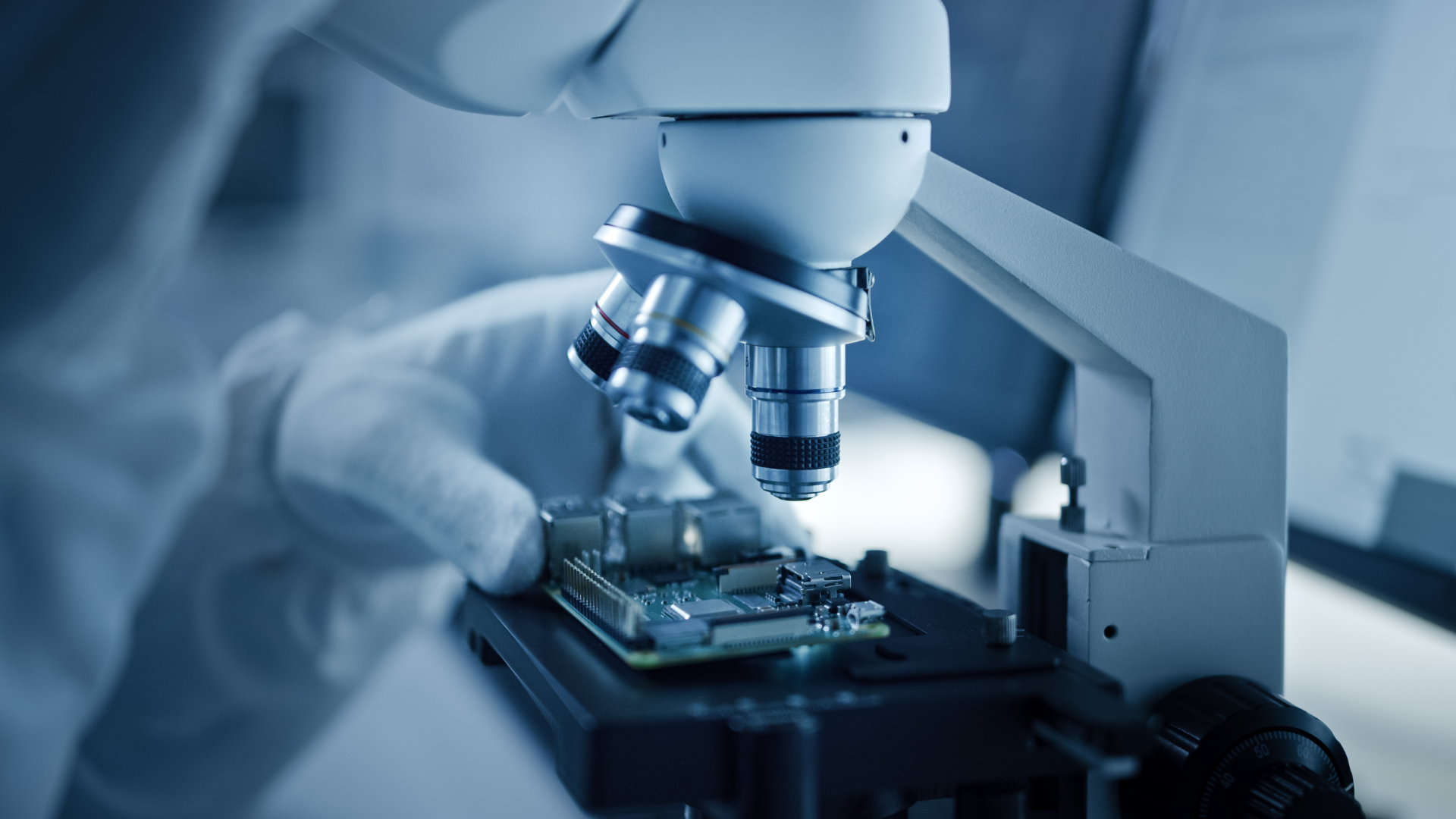
Reliability Testing
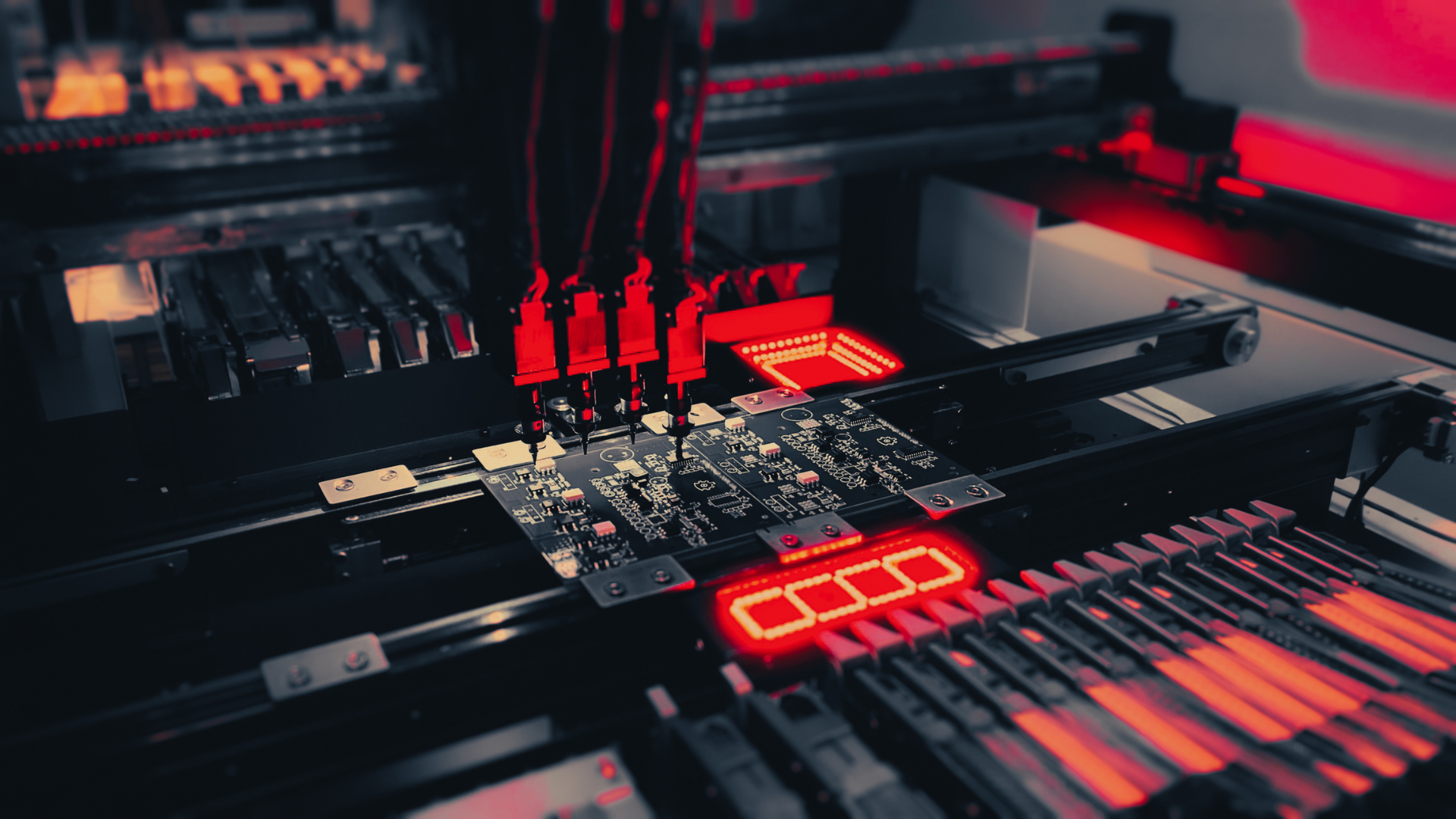
Machined Tools for Mass Production
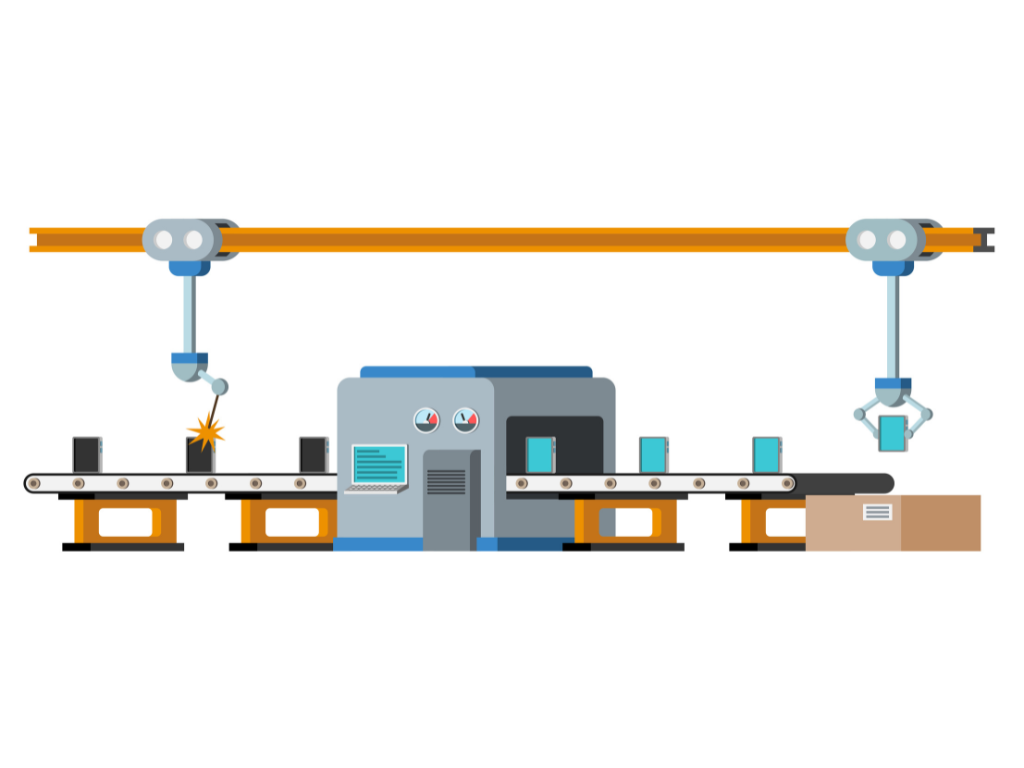
Packaging Design and Mass Production
In the early stages of product development, we understand the importance when it comes to validating the viability of a concept in a timely manner. Utilizing advanced prototyping and quick production techniques allows our customers to receive samples quickly to test their concepts internally and among potential users.
Before entering the mass production stage, the product will pass through various validation phases including EVT, DVT, and PVT, where the design is put through strenuous tests and with adjustments implemented that ensure the stability of subsequent manufacturing process and quality control.
Through prototyping and various engineering validation phases, we work closely with our customers to revise and finalize to meet standards, resulting in designs that will be ready for mass production with optimal yield.
Testing and Validation
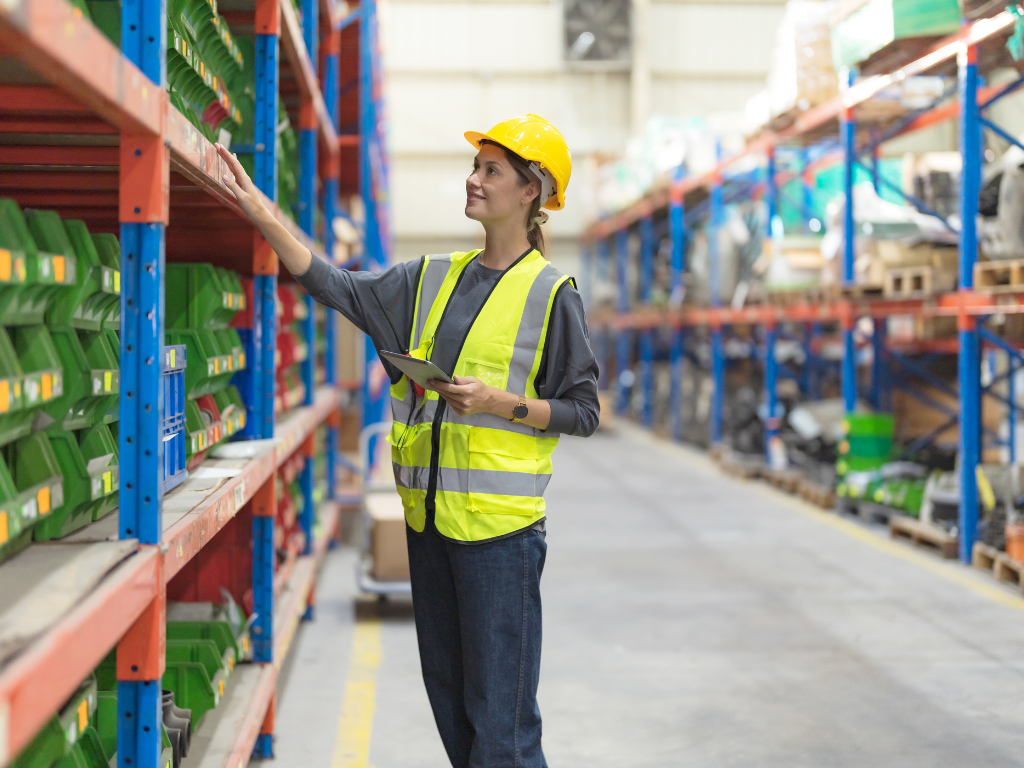
Basic Inspections
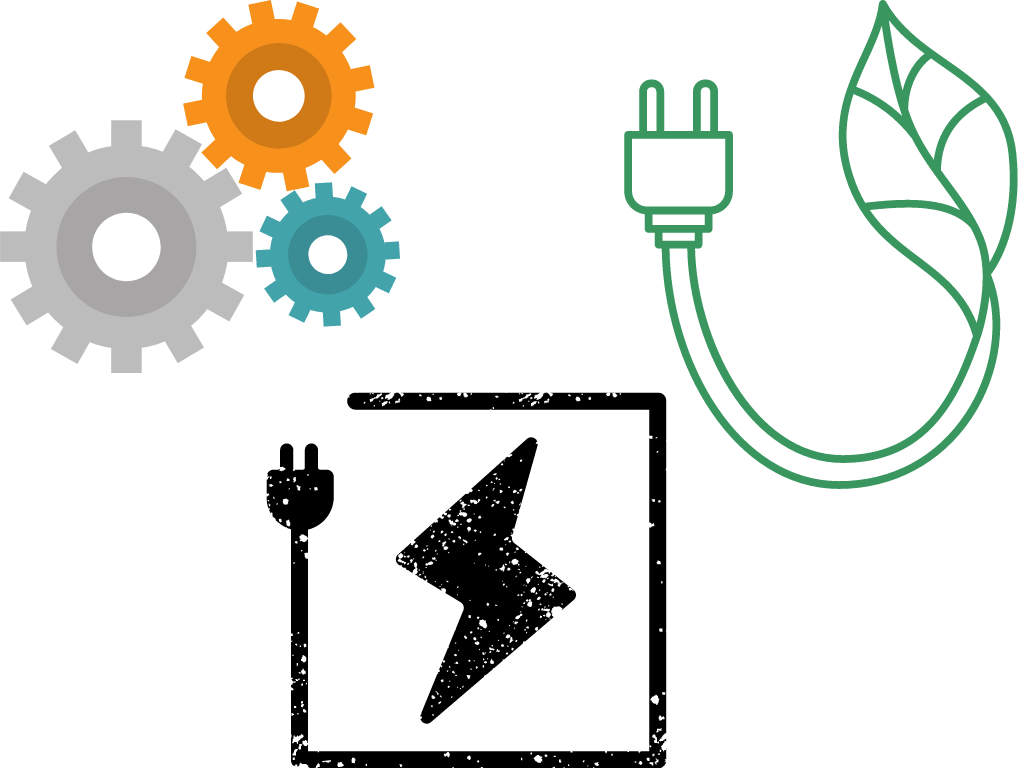
Environmental tests
Mechanical tests
Electrical tests
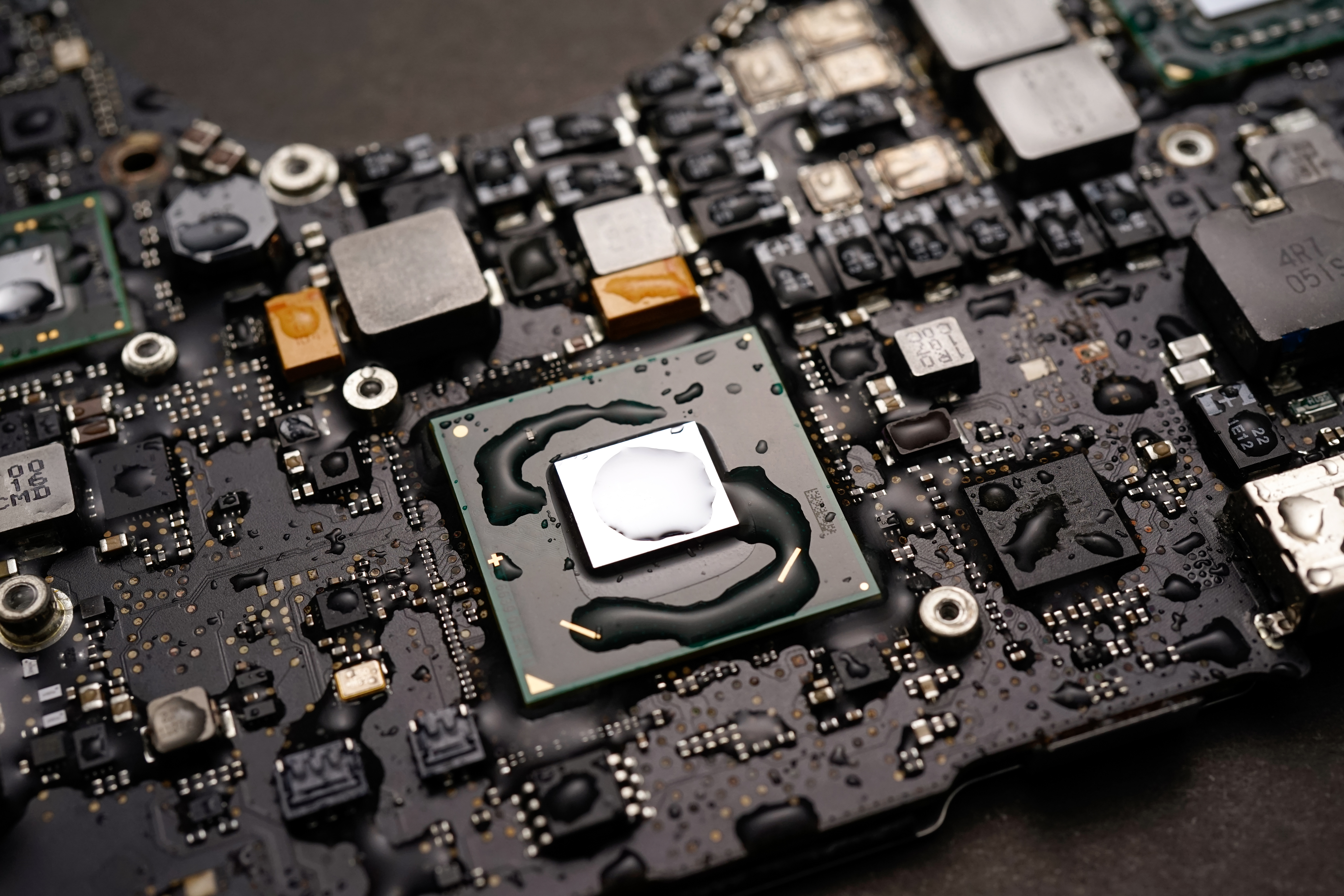
Waterproof tests
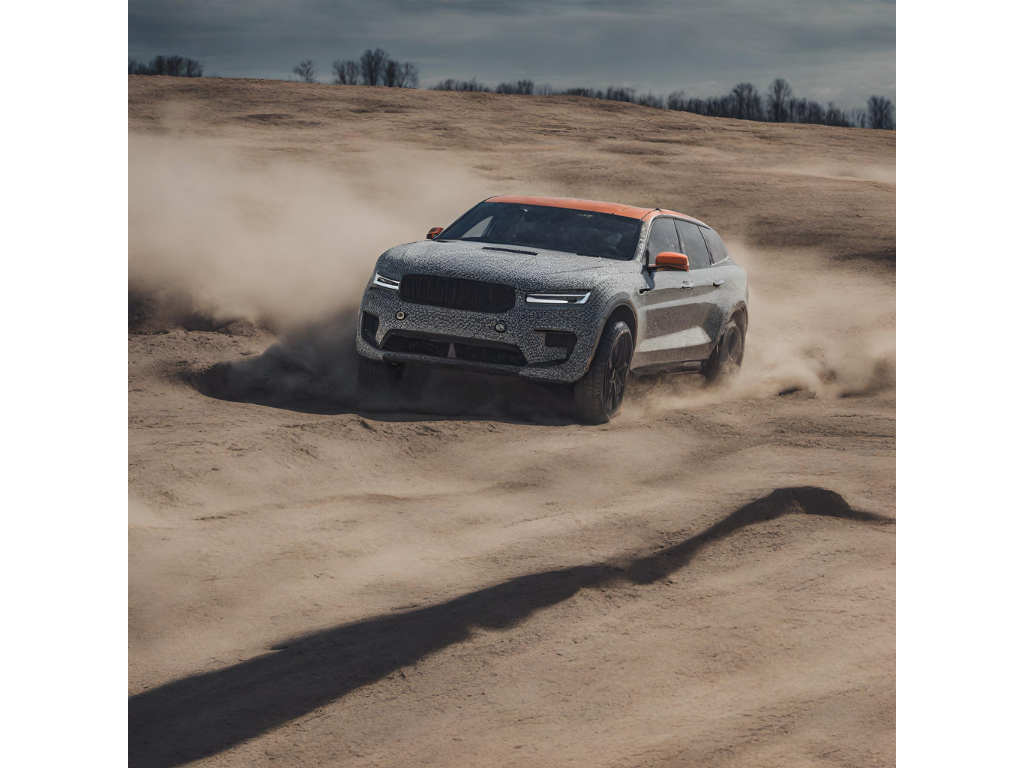
Outdoor Rugged Conditions Tests
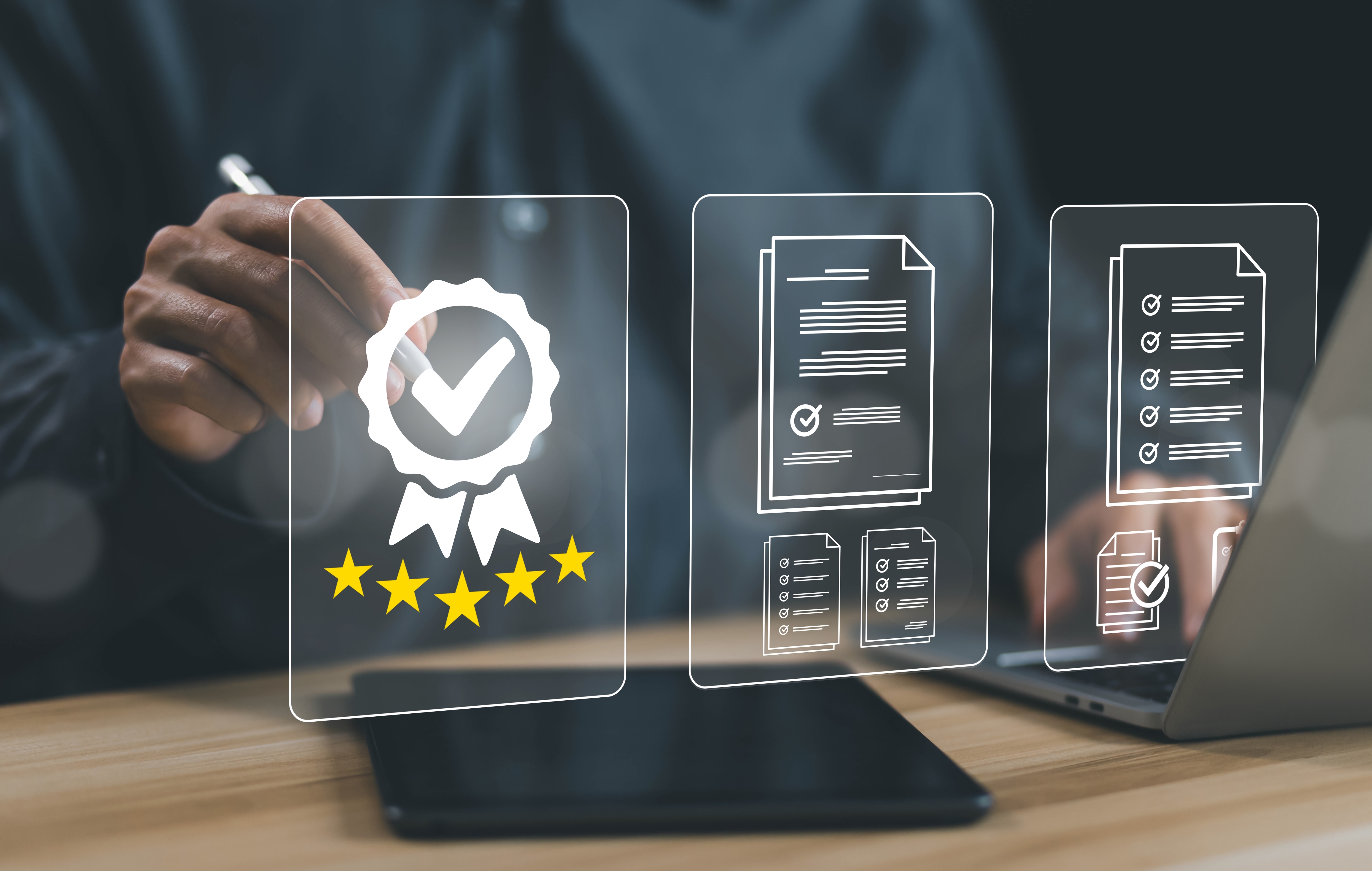
Compliance and Certifications
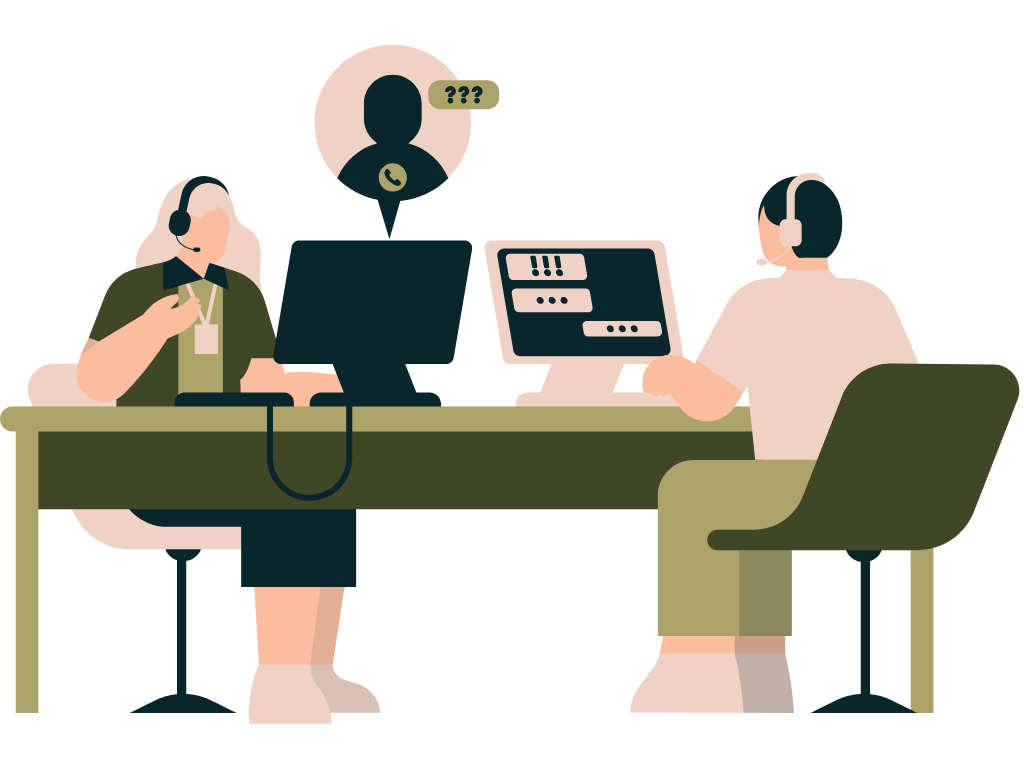
Specific or Customized Test Requirements
We understand the value that our customer puts into their product, and quality is what we strive for. Rayo supports managing all aspects of a product’s lifecycle from initial concept validation to bringing products to mass production.